Prozesssicherheit durch kontrollierte Späne
Prozesssicherheit durch kontrollierte Späne
Spanbildung und Spanabfuhr
Die Spanbildung ist das Ergebnis einer komplexen Wechselwirkung von Einflüssen auf die Zerspanung. Wesentliche Faktoren sind der Werkstoff, die Werkzeuggeometrie und die Schnittdaten. Dies zeigt sich beim Gewinden, Bohren und Fräsen. Anhand der Späneausformung werden hier auch Vibrationen erkannt.
Bei der Zerspanung mit definierter Schneide ist die Spanbildung von entscheidender Bedeutung. Nur ein „optimaler“ Span lässt sich gut abführen und ist damit Grundlage für einen sicheren Prozess. Läuft ein Prozess unzuverlässig, worauf schwankende Standzeiten hindeuten können, sind häufig die Späne die Ursache. Abhängig vom Zerspanungsverfahren stellt das die Werkzeugentwicklung und -konstruktion vor ebenso große wie spezifische Herausforderungen. Ungeachtet des Verfahrens ist es für Hersteller in jedem Fall aufwendig und kostenintensiv, die Werkzeugproduktion so zu gestalten, dass Reproduzierbarkeit gewährleistet ist. Und das über Jahre, zum Teil auch Jahrzehnte – so lange das Werkzeug marktgängig ist.
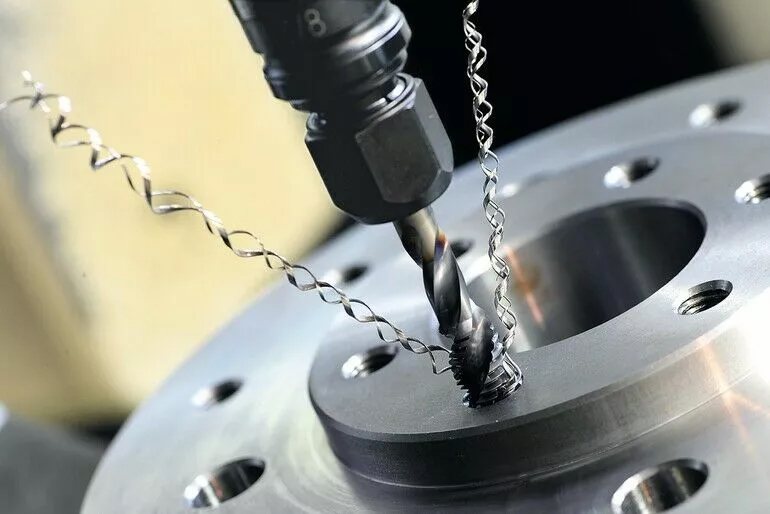
Je länger der Anschnitt ist beziehungsweise je mehr Nuten das Werkzeug hat, desto dünner wird der Spanquerschnitt. (Bild: OSG)
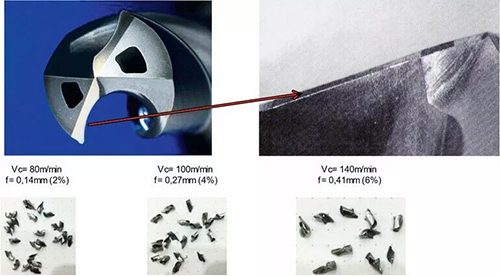
Gleichmäßige Spanbildung beim Bohren. (Bild: OSG)
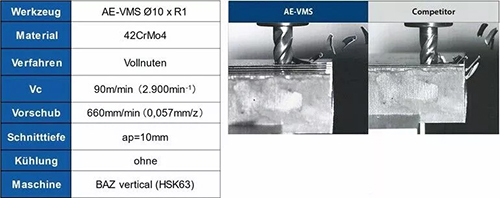
Das Nutdesign des „AE-VMS“-Fräsers bewirkt eine sehr gute Spanabfuhr, sogar beim Fräsen von Vollnuten. (Bild: OSG)
Spanbildung beim Gewinden
Das Problem beim Gewindebohren besteht darin, dass der Anwender nur einen Parameter – die Schnittgeschwindigkeit – beeinflussen kann. Der Vorschub ist dagegen durch die Gewindesteigung gegeben. Das hat zur Folge, dass die Spanbildung ausschließlich durch die Geometrie des Gewindebohrers beeinflusst wird. Man sollte meinen, dass dies keine große Herausforderung darstellt. Doch das Gegenteil ist der Fall: Aufgrund der Gestaltung des Anschnitts kommt es in diesem Bereich zu sehr unterschiedlichen Spanquerschnitten. Die Querschnitte wiederum beeinflussen maßgeblich die Spanbildung. Das bedeutet: Durch Anpassen der Nutform und der Schneidengeometrie muss der Span in die richtige Form gebracht werden. Ohne Know-how ist das nicht möglich.
Spanbildung beim Bohren
Beim Bohren besteht zusätzlich zur Schnittgeschwindigkeit die Möglichkeit, den Vorschub beliebig zu ändern. Entsteht zum Beispiel ein langer Span, kann versucht werden, mit Erhöhen des Vorschubs einen dickeren Span zu erzeugen, der entsprechend stärker gestaucht wird und kürzer bricht. Besser ist es jedoch, Geometrien gleich so zu entwickeln, dass stets ein kurzer Span entsteht – unabhängig von Schnittgeschwindigkeit und Vorschub, im besten Fall sogar unabhängig vom bearbeitenden Material. OSG betreibt große Anstrengungen in der Werkzeugentwicklung, um den Span über die Geometrie zu kontrollieren. Die Maschinen sind hierbei ebenso ausschlaggebend wie die Werkzeugaufnahme, die Spannsituation des Werkstücks, das Kühlmittel und das Werkstück selbst. Anwender können angesichts dieser komplexen Situation vor Ort die optimalen Schnittdaten nicht immer umsetzen.
Spanbildung beim Fräsen
Beim Fräsen liegt stets ein unterbrochener Schnitt vor. Man könnte daher meinen, dass die Spanbildung und Spanabfuhr nur eine geringe Gewichtung haben. Natürlich vereinfacht dies die Prozessführung, es ist aber kein Grund, dem Span weniger Aufmerksamkeit zu widmen. Auch beim Fräsen ist es wichtig, dass der Span gut abgeführt wird, nirgends liegenbleibt oder gar noch einmal mitgezogen wird. Gute Spanabfuhr setzt eine gute, gleichmäßige Spanbildung voraus. Beim Fräsen gibt der Span zu erkennen, ob die passenden Parameter gewählt wurden. Zudem lässt sich an den Anlassfarben ablesen, ob die Bearbeitungstemperatur über den Span abgeführt wird. Nicht zuletzt lassen sich am Span auch Vibrationen erkennen, die sich ungünstig auf die Werkzeugstandzeit und die Oberflächenqualität des Bauteils auswirken können. Grundsätzlich stellen sich beim Fräsen für den Anwender große Herausforderungen, da er nicht nur Schnittdaten wie die Schnittgeschwindigkeit oder dem Vorschub beeinflussen kann, sondern auch die Zustelltiefe, die Zustellbreite und die Bearbeitungsstrategie.
"Mit Vischer & Bolli wird immer ein Fortschritt erzielt!"
Niére Lousada, Leiter Werkzeugbau bei Ganahl AG.
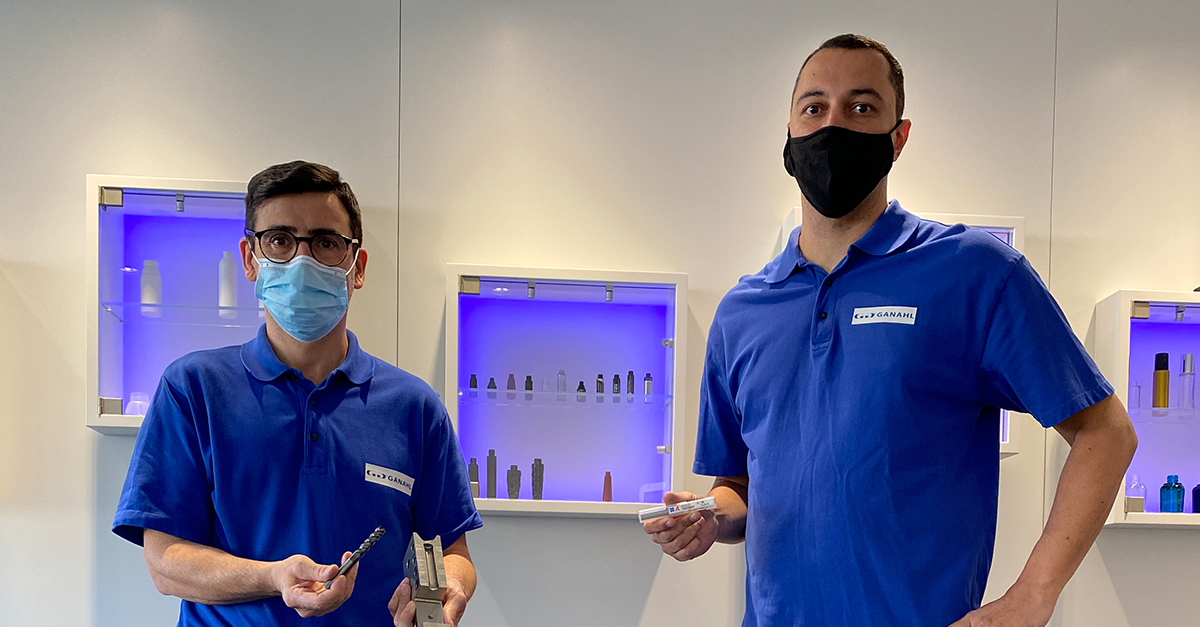
Foto links: José Martins - Werkzeugmacher /rechts: Niére Lousada - Leiter Werkzeugbau
Als Mitglied der HEINZ Glas Group entwickeln, produzieren und liefern sie pro Jahr mehr als 200 Millionen Teile hochwertiger Kosmetik- und Parfumflakons an ihre Kunden in der ganzen Welt.
Für die Entwicklung und Herstellung von Spritzblas-Werkzeugen haben sie mehrere Bohr- und Fräswerkzeuge von vb-tools im Einsatz – insbesondere der AE-VML Fräser von OSG. Dieses Werkzeug ist in ihrer Bearbeitungsstrategie nicht mehr wegzudenken, denn der AE-VML hat die passende Dimension, garantiert Prozesssicherheit und ist langlebig. Die Standzeit mit diesem Werkzeug konnte von 80 min auf 112 min gesteigert werden. Herr Lousada kann das Werkzeug jedem Fertigungsbetrieb, welches Trochoidalfräsen betreibt, weiterempfehlen.
Zum Unternehmen Ganahl AG:
Mit unseren selbst entwickelten und gefertigten Spritzblasmaschinen (IBM) und Blasformwerkzeugen produzieren wir Flaschen, Behälter und Gefässe mit einem Fassungsvermögen von 1,5 ml bis 250 ml aus allen gängigen Thermoplasten in ausgezeichneter Qualität.
Bei der Umsetzung komplexer Aufgaben setzen wir unsere zuverlässigen Maschinen und Werkzeuge, die aus unserer hauseigenen Entwicklung und Fertigung stammen, in Kombination mit unserem umfassenden Prozess Wissen ein. Unsere Kunden profitieren von der hohen Präzision und Qualität unserer Fertigungsprozesse, die mit unserer tief verwurzelten Erfahrung gekoppelt sind.